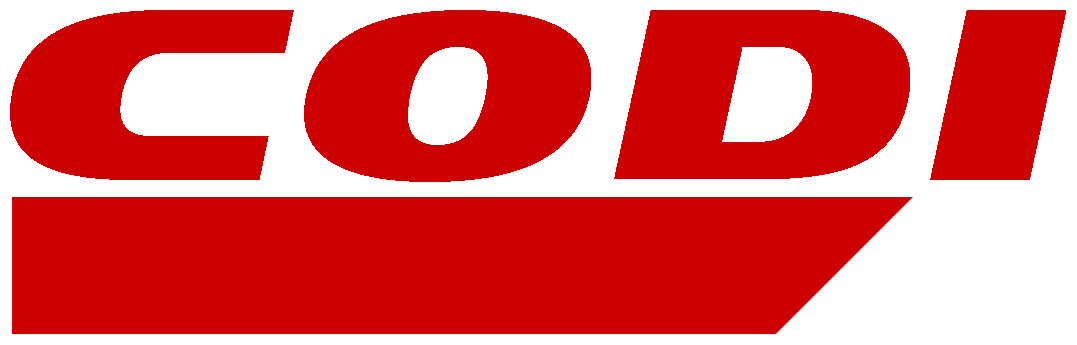
Craft Canning System
How To Design a Craft Canning System
Design Your Canning System for Success!
Determining the Footprint of a Canning System
What is your size?
Careful planning is encouraged when picking a canning line. Knowing your space limitations, future plans for expansion, and daily production requirements will impact your choice of the size of the craft canning system needed to reach your goals.
- How much space is available for a beverage canning system?
- Will the line be permanently mounted or be moved in and out?
- Logistics - How will unfilled cans be brought into the productions space and filled cans stored with minimal handling.
- What type of drainage is in place?
- What type of auxiliary equipment is needed to support the canning line and is there enough space allotted for installation of these items?
- Power requirements
- Carbon Dioxide requirements
- Compressed air requirements
- Has a plan for future growth been considered?
Once these questions are answered, it is wise to start working with an engineering firm to help design an efficient and cost effective layout of the desired canning system.
Quality Canning
Quality Fill for a Quality Product
Quality Output is important when selecting a filler. Cases of poorly filled cans due to bad seam quality, lower carbonation, low fills, etc. will do no benefit to a brewery or mobile canning operation. Save the frustration by doing your research and choosing a filler that meets your needs with a reliable, repeatable, quality, counter pressure fill.
Look for the following items when choosing a filler.
- PLC Controlled Filling - Ability to adjust everything from the HMI and save recipes. Creates consistency between canning runs.
- Controlling Purge Cycles, Fill Rate, Snift
- Cleansing cans prior to filling through a twist rinse utilizing either water or ionized air
- Reduced time between filling and seaming processes. Try to find a filler that utilizes a seamer that is faster to reduce exposure to outside elements.
- Automatic can end placement and missing lid detection which saves cans from jamming in machines.
- Mechanically engaged seaming operations
- It is good practice to monitor seams during production runs at least 3 times. Once at the beginning, once half way through the run, and finally one more check at the end of the run.
- This three time test procedure will help reduce loss if there is an issue with the canner during a run.
- Because this is a packaged product that the public is consuming, practices like wearing hair and beard nets, gloves, and safety glasses should be followed closely. Looking around online there are countless videos of packing lines where clean practices are neglected. Some even show bare hands and fingers inside of cans prior to filling.
Desired Output
How much can you can?
Fillers can vary greatly when it comes to fill type and output and choosing the correct one for your application is very important. Step one to choosing a filler is knowing how many cans per minute can be filled. Once the desired output is selected, considering what filler is right for the application is much easier.
Many breweries in the craft beer industry start the voyage into canning by hiring a Mobile Canning company to come in and can their product before actually purchasing a filler of their own. This can be a good way to test the waters of canning and distributing product beyond the tap room. Most breweries that start with Mobile Canning eventually purchase a comparable or slightly larger capacity Filler and implement a full time canning system.
Filler Output Made Easy
Know Your Output Potential
25 CPM = 4.55 bbl/hr
15 Barrels canned in under 4 hours
50 CPM = 9.09 bbl/hr
60 Barrels canned in under 7 hours
100 CPM = 18.18 bbl/hr
60 Barrels canned in under 4 hours
250 CPM = 45.45 bbl/hr
120 Barrels canned in under 3 hours
Evaluating Canning System Suppliers
A quality product deserves a quality system.
Choose a System Supplier
Who can supply a Craft Canning System?
Beyond choosing the quality design, quality cleanability, and quality canning, determining which supplier to choose can be impacted by hidden costs and other factors.
- Does the supplier design, manufacture, and supply a complete system?
- What is the lead time for the system?
- What are your crating and shipping costs?
- Has the system been specially engineered to your facility?
Creating a Packaging Line Layout
Follow these steps
Determine if a Depalletizer is Required
Feed the Filler
Depalletizing cans increases throughput and eliminates labor from the packaging floor which is a great way to free up employees to be useful elsewhere in the brewery. When deciding on a Craft Can Depalletizer, all-around functionality, integrated safety features, and standard design should be considered when looking at these machines.
Start by looking at the standard design of the equipment. Basic features to look for include an easy to use interface, safety minded design features, filler to depalletizer communication, and proper hardware use above open cans. Choosing a supplier that engineers features like these into the design of the machine is important to good production and general workplace safety.
The functionality of a can depalletizer is critical to productive packaging runs.
- Integrated Light Curtain Safety Fence
- Belt Driven not center all thread moving above open cans
- Not dragging slip sheet across remaining cans
- Integrated Slip Sheet Stacking - minimize floor space
- Minimal moving parts directly above cans
- Easy to operate touchscreen user interface
- VFD controlled motors
- Integrated Platform
As the end user you are responsible safety within your facility in the USA and not having integrated safety to stop the hoist only exposes you to a lost time accident.
Other items to consider would be how far away the depalletizer is from the filler. Does the manufacturer also design conveyance to work seamlessly with the depalletizer? Line integration problems can plague an owner for the life of the canning system. Solving these sort of issues up front will be beneficial in the long run.
Select a Filler
Get the product into the Can
Selecting the right beverage can filler is the first step of the equipment selection process for any canning system. Counter Pressure Fillers versus Open Air Fillers, cleanability of the canning system, and mechanical engagement of seaming operations are the three most important aspects to consider when choosing a canning system.
Counter pressure technology offers the ability to easily package product with higher carbonation and lower dissolved oxygen.
Cleanability of a machine is how well you can sanitize the equipment between canning runs. The problems of canning with a dirty machine can include off flavors and inconsistencies in packaged products.
Mechanical Engagement of Critical Seaming Operations ensures that your packaged product is done properly and drops in air pressure haven’t compromised seam quality.
Not all canners are created equal and are priced accordingly – To get a fair comparison take the total price of the canning system divided by cans per minute (CPM) and it will give you the CPM per dollar invested.
Connecting Equipment with Conveyance
Going from Start to Finish
In any beverage filling application, the conveyance should meet standard design practices for food and beverage transport and the following features should be strongly considered when choosing a conveyance supplier.
- Stainless steel components with washdown duty bearings and motors
- All fasteners are secured with lock washers or locking nuts
- Conveyor side rails are spaced away from the frame to allow for easy cleaning
- Washout Flaps for easy access and ability to clean the internals of the conveyance
- Wet can blow off system
- Stainless steel drip pans with threaded half coupling
- Stainless steel motor housings with washdown duty coatings and seals
When a Automated Packer Should Be Considered
Pack it out!
Manual pack out versus automated pack out depends highly on the output of the filler. There is not much of a need to use a packer for a canning system running less than 30 cans per minute. The same can be said for using manual pack-out labor for a canning system running more than 100 cans per minute. It just does not make sense to pay labor wages when a machine can do the work of 2 or 3 employees.
Craft Canning Equipment
Click below to learn more
© 2016